A Users Guide to Vacuum Technology
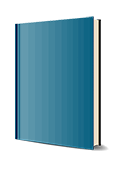
4. Auflage Oktober 2023
576 Seiten, Hardcover
Lehrbuch
A USERS GUIDE TO VACUUM TECHNOLOGY
Choose and understand the vacuum technology that fits your project's needs with this indispensable guide
Vacuum technology is used to provide process environments for other kinds of engineering technology, making it an unsung cornerstone of hundreds of projects incorporating analysis, research and development, manufacturing, and more. Since it is very often a secondary technology, users primarily interested in processes incorporating it will frequently only encounter vacuum technology when purchasing or troubleshooting. There is an urgent need for a guide to vacuum technology made with these users in mind.
For decades, A User's Guide to Vacuum Technology has met this need, with a user-focused introduction to vacuum technology as it is incorporated into semiconductor, optics, solar sell, and other engineering processes. With an emphasis on otherwise neglected subjects and on accessibility to the secondary user of vacuum technology, it balances treatment of older systems that are still in use with a survey of the latest cutting-edge technologies. The result promises to continue as the essential guide to vacuum systems.
Readers of the fourth edition of A User's Guide to Vacuum Technology will also find:
* Expanded treatment of gauges, pumps, materials, systems, and best??operating practices
* Detailed discussion of cutting-edge topics like ultraclean vacuum and contamination control
* An authorial team with decades of combined research and engineering experience
A User's Guide to Vacuum Technology is essential for those entering emerging STEM programs, engineering professionals and graduate students working with a huge range of engineering technologies.
Symbols xix
Part I Its Basis 1
1 Vacuum Technology 3
1.1 Units of Measurement 8
References 9
2 Gas Properties 11
2.1 Kinetic Picture of a Gas 11
2.1.1 Velocity Distribution 12
2.1.2 Energy Distribution 13
2.1.3 Mean Free Path 14
2.1.4 Particle Flux 15
2.1.5 Monolayer Formation Time 15
2.1.6 Pressure 16
2.2 Gas Laws 16
2.2.1 Boyle's Law 17
2.2.2 Amontons' Law 17
2.2.3 Charles' Law 18
2.2.4 Dalton's Law 18
2.2.5 Avogadro's Law 18
2.2.6 Graham's Law 19
2.3 Elementary Gas Transport Phenomena 19
2.3.1 Viscosity 19
2.3.2 Thermal Conductivity 22
2.3.3 Diffusion 23
2.3.4 Thermal Transpiration 24
References 25
3 Gas Flow 27
3.1 Flow Regimes 27
3.2 Flow Concepts 29
3.3 Continuum Flow 31
3.3.1 Orifice 32
3.3.2 Long Round Tube 34
3.3.3 Short Round Tube 36
3.4 Molecular Flow 37
3.4.1 Orifice 38
3.4.2 Long Round Tube 39
3.4.3 Short Round Tube 39
3.4.4 Irregular Structures 41
3.4.4.1 Analytical Solutions 42
3.4.4.2 Statistical Solutions 43
3.4.5 Components in Parallel and Series 43
3.5 Models Spanning Molecular and Viscous Flow 53
References 55
4 Gas Release from Solids 59
4.1 Vaporization 59
4.2 Diffusion 60
4.2.1 Reduction of Outdiffusion by Vacuum Baking 62
4.3 Thermal Desorption 63
4.3.1 Zero Order 63
4.3.2 First Order 64
4.3.3 Second Order 65
4.3.4 Desorption from Real Surfaces 67
4.3.5 Outgassing Measurements 67
4.3.6 Outgassing Models 69
4.3.7 Reduction by Baking 69
4.4 Stimulated Desorption 71
4.4.1 Electron-Stimulated Desorption 71
4.4.2 Ion-Stimulated Desorption 71
4.4.3 Stimulated Chemical Reactions 72
4.4.4 Photo Desorption 72
4.5 Permeation 73
4.5.1 Atomic and Molecular Permeation 73
4.5.2 Dissociative Permeation 74
4.5.3 Permeation and Outgassing Units 75
4.6 Pressure Limitations During Pumping 76
References 78
Part II Measurement 81
5 Pressure Gauges 83
5.1 Direct Reading Gauges 83
5.1.1 Diaphragm and Bourdon Gauges 84
5.1.2 Capacitance Manometer 85
5.2 Indirect Reading Gauges 88
5.2.1 Thermal Conductivity Gauges 88
5.2.1.1 Pirani Gauge 90
5.2.1.2 Thermocouple Gauge 91
5.2.1.3 Stability and Calibration 92
5.2.2 Spinning Rotor Gauge 93
5.2.3 Ionization Gauges 95
5.2.3.1 Hot Cathode Gauges 95
5.2.3.2 Hot Cathode Gauge Errors 100
5.2.3.3 Cold Cathode Gauge 103
5.2.3.4 Gauge Calibration 105
References 105
6 Flow Meters 109
6.1 Molar Flow, Mass Flow, and Throughput 109
6.2 Rotameters and Chokes 111
6.3 Differential Pressure Devices 112
6.4 Thermal Mass Flow Technique 114
6.4.1 Mass Flow Meter 114
6.4.2 Mass Flow Controller 117
6.4.3 Mass Flow Meter Calibration 119
References 119
7 Pumping Speed 121
7.1 Definition 121
7.2 Mechanical Pump Speed Measurements 122
7.3 High Vacuum Pump Speed Measurements 123
7.3.1 Methods 123
7.3.2 Gas and Pump Dependence 124
7.3.3 Approximate Speed Measurements 125
7.3.4 Errors 125
References 127
8 Residual Gas Analyzers 129
8.1 Instrument Description 129
8.1.1 Ion Sources 131
8.1.1.1 Open Ion Sources 131
8.1.1.2 Closed Ion Sources 133
8.1.2 Mass Filters 134
8.1.2.1 Magnetic Sector 134
8.1.2.2 RF Quadrupole 135
8.1.2.3 Resolving Power 138
8.1.3 Detectors 138
8.1.3.1 Discrete Dynode Electron Multiplier 139
8.1.3.2 Continuous Dynode Electron Multiplier 140
8.2 Installation and Operation 142
8.2.1 Operation at High Vacuum 142
8.2.1.1 Sensor Mounting 142
8.2.1.2 Stability 143
8.2.2 Operation at Medium and Low Vacuum 145
8.2.2.1 Differentially Pumped Analysis 145
8.2.2.2 Miniature Quadrupoles 148
8.3 Calibration 148
8.4 Choosing an Instrument 149
References 150
9 Interpretation of RGA Data 153
9.1 Cracking Patterns 153
9.1.1 Dissociative Ionization 153
9.1.2 Isotopes 154
9.1.3 Multiple Ionization 154
9.1.4 Combined Effects 154
9.1.5 Ion-Molecule Reactions 157
9.2 Qualitative Analysis 158
9.3 Quantitative Analysis 163
9.3.1 Isolated Spectra 164
9.3.2 Overlapping Spectra 165
References 169
Part III Production 171
10 Mechanical Pumps 173
10.1 Rotary Vane 173
10.2 Lobe 177
10.3 Claw 180
10.4 Multistage Lobe 182
10.5 Scroll 184
10.6 Screw 185
10.7 Diaphragm 185
10.8 Reciprocating Piston 187
10.9 Mechanical Pump Operation 189
References 189
11 Turbomolecular Pumps 191
11.1 Pumping Mechanism 191
11.2 Speed-Compression Relations 192
11.2.1 Maximum Compression 193
11.2.2 Maximum Speed 195
11.2.3 General Relation 197
11.3 Ultimate Pressure 198
11.4 Turbomolecular Pump Designs 199
11.5 Turbo-Drag Pumps 201
References 203
12 Diffusion Pumps 205
12.1 Pumping Mechanism 205
12.2 Speed-Throughput Characteristics 207
12.3 Boiler Heating Effects 211
12.4 Backstreaming, Baffles, and Traps 212
References 215
13 Getter and Ion Pumps 217
13.1 Getter Pumps 217
13.1.1 Titanium Sublimation 218
13.1.2 Non-evaporable Getters 223
13.2 Ion Pumps 224
References 229
14 Cryogenic Pumps 233
14.1 Pumping Mechanisms 234
14.2 Speed, Pressure, and Saturation 237
14.3 Cooling Methods 241
14.4 Cryopump Characteristics 245
14.4.1 Sorption Pumps 246
14.4.2 Gas Refrigerator Pumps 249
14.4.3 Liquid Cryogen Pumps 253
References 253
Part IV Materials 257
15 Materials in Vacuum 259
15.1 Metals 260
15.1.1 Vaporization 260
15.1.2 Permeability 260
15.1.3 Outgassing 261
15.1.3.1 Dissolved Gas 262
15.1.3.2 Surface and Near-Surface Gas 264
15.1.4 Structural Metals 269
15.2 Glasses and Ceramics 272
15.3 Polymers 277
References 281
16 Joints Seals and Valves 285
16.1 Permanent Joints 285
16.1.1 Welding 286
16.1.2 Soldering and Brazing 290
16.1.3 Joining Glasses and Ceramics 291
16.2 Demountable Joints 293
16.2.1 Elastomer Seals 294
16.2.2 Metal Gaskets 300
16.3 Valves and Motion Feedthroughs 302
16.3.1 Small Valves 302
16.3.2 Large Valves 304
16.3.3 Special-Purpose Valves 307
16.3.4 Motion Feedthroughs 308
References 313
17 Pump Fluids and Lubricants 315
17.1 Pump Fluids 315
17.1.1 Fluid Properties 315
17.1.1.1 Vapor Pressure 316
17.1.1.2 Other Characteristics 319
17.1.2 Fluid Types 319
17.1.2.1 Mineral Oils 320
17.1.2.2 Esters 321
17.1.2.3 Silicones 321
17.1.2.4 Ethers 322
17.1.2.5 Fluorochemicals 322
17.1.3 Selecting Fluids 323
17.1.3.1 Rotary, Vane, and Lobe Pump Fluids 323
17.1.3.2 Turbo Pump Fluids 325
17.1.3.3 Diffusion Pump Fluids 325
17.1.4 Reclamation 328
17.2 Lubricants 328
17.2.1 Lubricant Properties 329
17.2.1.1 Absolute Viscosity 330
17.2.1.2 Kinematic Viscosity 331
17.2.1.3 Viscosity Index 332
17.2.2 Selecting Lubricants 333
17.2.2.1 Liquid 333
17.2.2.2 Grease 334
17.2.2.3 Solid Film 336
References 338
Part V Systems 341
18 Rough Vacuum Pumping 343
18.1 Exhaust Rate 344
18.1.1 Pump Size 344
18.1.2 Aerosol Formation 346
18.2 Crossover 350
18.2.1 Minimum Crossover Pressure 351
18.2.2 Maximum Crossover Pressure 354
18.2.2.1 Diffusion 354
18.2.2.2 Turbo 357
18.2.2.3 Cryo 357
18.2.2.4 Sputter-Ion 360
References 362
19 High Vacuum Systems 365
19.1 Diffusion-Pumped Systems 365
19.1.1 Operating Modes 368
19.1.2 Operating Issues 369
19.2 Turbo-Pumped Systems 371
19.2.1 Operating Modes 374
19.2.2 Operating Issues 375
19.3 Sputter-Ion-Pumped Systems 376
19.3.1 Operating Modes 377
19.3.2 Operating Issues 379
19.4 Cryo-Pumped Systems 379
19.4.1 Operating Modes 380
19.4.2 Regeneration 380
19.4.3 Operating Issues 382
19.5 High Vacuum Chambers 383
19.5.1 Managing Water Vapor 384
References 386
20 Ultraclean Vacuum Systems 387
20.1 Ultraclean Pumps 389
20.1.1 Dry Roughing Pumps 390
20.1.2 Turbopumps 390
20.1.3 Cryopumps 390
20.1.4 Sputter-Ion, TSP, and NEG Pumps 391
20.2 Ultraclean Chamber Materials and Components 392
20.3 Ultraclean System Pumping and Pressure Measurement 394
References 398
21 Controlling Contamination in Vacuum Systems 401
21.1 Defining Contamination in a Vacuum Environment 401
21.1.1 Establishing Control of Vacuum Contamination 401
21.1.2 Types of Vacuum Contamination 402
21.1.2.1 Particle Contamination 403
21.1.2.2 Gas Contamination 409
21.1.2.3 Film Contamination 410
21.2 Pump Contamination 411
21.2.1 Low/Rough and Medium Vacuum Pump Contamination 411
21.2.1.1 Fluid-Sealed Mechanical Pumps 412
21.2.1.2 Dry Mechanical Pumps 413
21.2.2 High and UHV Vacuum Pump Contamination 415
21.2.2.1 Diffusion Pumps 416
21.2.2.2 Turbo- and Turbo-Drag Pumps 417
21.2.2.3 Cryopumps 418
21.2.2.4 Sputter-Ion and Titanium-Sublimination Pumps 419
21.3 Evacuation Contamination 420
21.3.1 Particle Sources 420
21.3.2 Remediation Methods 421
21.4 Venting Contamination 422
21.5 Internal Components, Mechanisms, and Bearings 423
21.6 Machining Contamination 426
21.6.1 Cutting, Milling, and Turning 426
21.6.2 Grinding and Polishing 427
21.6.3 Welding 428
21.7 Process-Related Sources 429
21.7.1 Deposition Sources 429
21.7.2 Leak Detection 430
21.8 Lubrication Contamination 432
21.8.1 Liquid Lubricants 432
21.8.2 Solid Lubricants 433
21.8.3 Lamellar, Polymer, and Suspension Lubricants 434
21.9 Vacuum System and Component Cleaning 434
21.9.1 Designing a Cleaning Process 435
21.10 Review of Clean Room Environments for Vacuum Systems 436
21.10.1 The Cleanroom Environment 438
21.10.2 Using Vacuum Systems in a Cleanroom Environment 438
References 442
22 High Flow Systems 445
22.1 Mechanically Pumped Systems 447
22.2 Throttled High Vacuum Systems 449
22.2.1 Chamber Designs 449
22.2.2 Turbo Pumped 451
22.2.3 Cryo Pumped 455
References 459
23 Multichambered Systems 461
23.1 Flexible Substrates 462
23.2 Rigid Substrates 465
23.2.1 Inline Systems 465
23.2.2 Cluster Systems 469
23.3 Analytical Instruments 472
References 472
24 Leak Detection 475
24.1 Mass Spectrometer Leak Detectors 476
24.1.1 Forward Flow 476
24.1.2 Counter flow 477
24.2 Performance 478
24.2.1 Sensitivity 478
24.2.2 Response Time 480
24.2.3 Testing Pressurized Chambers 481
24.2.4 Calibration 482
24.3 Leak Hunting Techniques 483
24.4 Leak Detecting with Hydrogen Tracer Gas 486
References 487
Part VI Appendices 489
Appendix A Units and Constants 491
Appendix B Gas Properties 495
Appendix C Material Properties 509
Appendix D Isotopes 519
Appendix E Cracking Patterns 525
Appendix F Pump Fluid Properties 535
Index 543
Timothy A. Gessert, PhD, is Principal Scientist and Managing Member of Gessert Consulting, LLC, USA, former Principal Scientist at the National Renewable Energy Laboratory, USA, and Fellow and Past President of the AVS. He has published extensively on vacuum technology and related subjects.