Corrosion and Materials Selection
A Guide for the Chemical and Petroleum Industries
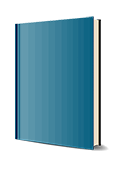
1. Auflage Juli 2014
576 Seiten, Hardcover
Wiley & Sons Ltd
The petroleum and chemical industries contain a wide variety of corrosive environments, many of which
are unique to these industries. Oil and gas production operations consume a tremendous amount of iron
and steel pipe, tubing, pumps, valves, and sucker rods. Metallic corrosion is costly. However, the cost of
corrosion is not just financial. Beyond the huge direct outlay of funds to repair or replace corroded structures are the indirect costs - natural resources, potential hazards, and lost opportunity. Wasting natural resources is a direct contradiction to the growing need for sustainable development.
By selecting the correct material and applying proper corrosion protection methods, these costs can be
reduced, or even eliminated. This book provides a minimum design requirement for consideration when
designing systems in order to prevent or control corrosion damage safely and economically, and addresses:
* Corrosion problems in petroleum and chemical industries
* Requirements for corrosion control
* Chemical control of corrosive environments
* Corrosion inhibitors in refineries and petrochemical plants
* Materials selection and service life of materials
* Surface preparation, protection and maintainability
* Corrosion monitoring - plant inspection techniques and laboratory corrosion testing techniques
Intended for engineers and industry personnel working in the petroleum and chemical industries, this book is also a valuable resource for research and development teams, safety engineers, corrosion specialists and researchers in chemical engineering, engineering and materials science.
Preface xxiii
Acknowledgements xxv
1. Fundamentals of Corrosion in the Oil, Gas, and Chemical Industries 1
1.1 Uniform Corrosion 2
1.2 Localized Corrosion 3
1.3 Low-Temperature Corrosion 6
1.4 High-Temperature Corrosion 12
2. Corrosion Problems in the Petroleum and Chemical Industries 17
2.1 Stress Corrosion Cracking and Embrittlement 17
2.2 Hydrogen Attack 30
2.3 Corrosion Fatigue 33
2.4 Liquid-Metal Embrittlement 33
2.5 Basic Definition of Erosion-Corrosion 35
2.6 Mixed-Phase Flow 35
2.7 Entrained Catalyst Particles 36
2.8 Systematic Analysis of Project 36
2.9 Forms of Corrosion and Preventive Measures 43
2.10 Selective Leaching or De-Alloying Corrosion 49
2.11 Erosion-Corrosion 50
2.12 Stress Corrosion Cracking 52
2.13 Types of Hydrogen Damage 54
2.14 Concentration Cell Corrosion 55
2.15 Filiform Corrosion 56
2.16 Types of Intergranular Corrosion 56
2.17 Microbiologically Influenced Corrosion 57
2.18 Corrosion in Concrete 58
3. Corrosion Considerations in Material Selection 61
3.1 Corrosion in Oil and Gas Products 61
3.2 Corrosives and Corrosion Problems in Refineries and Petrochemical Plants 74
4. Engineering Materials 89
4.1 The Range of Materials 89
4.2 Properties of Engineering Materials 89
4.3 Corrosion Prevention Measures 91
4.4 Material Selection Procedure 93
4.5 Guidelines on Material Selection 93
4.6 Procedure for Material Selection 96
4.7 Process Parameters 97
4.8 Corrosion Rate and Corrosion Allowances 97
4.9 Corrosion Allowance 100
4.10 Selection of Corrosion-Resistance Alloys 100
4.11 Economics in Material Selection 102
4.12 Materials Appreciation and Optimization 103
4.13 Corrosion in Oil and Gas Products 104
4.14 Engineering Materials 105
4.15 Cast Iron 112
4.16 Non-Ferrous Metals 113
4.17 Polymers 116
4.18 Ceramics and Glasses 120
4.19 Composite Materials 123
5. Chemical Control of Corrosive Environments 125
5.1 General Requirements and Rules for Corrosion Control 125
5.2 Basic Types of Inhibitors and How They Work 127
5.3 Corrosive Environments 137
5.4 Techniques for the Application of Inhibitors 139
5.5 Inhibitor Mechanisms 140
5.6 Criteria for Corrosion Control by Inhibitors 141
5.7 System Condition 141
5.8 Selection of Inhibitors 143
5.9 Economics of Inhibition 150
5.10 Environmental Factors for Corrosion Inhibitor Applications 151
6. Requirements for Corrosion Control in the Petroleum and Petrochemical Industries 159
6.1 Exploration 159
6.2 Production 167
6.3 System Requirements for Corrosion Control of Oil Fields by Inhibitors 169
6.4 Types of Inhibitor 172
6.5 Selection of Inhibitor 173
6.6 Measurement 174
6.7 Factors Governing Oil Well Corrosion 175
6.8 Application of Inhibitor 177
6.9 Water Flooding and Water Disposal 181
6.10 Transportation and Storage 181
6.11 Biological Control in Oil and Gas Systems 183
6.12 Scale Control in Oil Systems 185
7. Corrosion Inhibitors in Refineries and Petrochemical Plants 205
7.1 Nature of Corrosive Fluids 205
7.2 Corrosion of Steel 206
7.3 Corrosion of Copper Alloys 207
7.4 Neutralizing Corrosion Inhibitors 207
7.5 Filming Inhibitors 208
7.6 Special Concepts in the Use of Corrosion Inhibitors in Refineries 209
7.7 Economic Aspects of Chemical Inhibition and Other Measures for Corrosion Prevention 210
7.8 Special Refinery Processes Amenable to Corrosion Inhibitors 211
7.9 Corrosion in Gas Processing Units 212
7.10 Miscellaneous Refinery Corrosion Problems 213
7.11 Selection of Inhibitor 214
7.12 Control of Fouling 214
7.13 Utility (Cooling Water and Boiler Systems) 218
7.14 Boiler Corrosion Problems 221
7.15 Treatment of Acid Systems 235
7.16 Chemical Cleaning of Process Equipment 237
7.17 Critical Equipment Areas 239
7.18 Identification of Deposits 239
7.19 Chemical Cleaning 242
8. Corrosion Inhibitor Evaluations 247
8.1 On-Line Monitoring of Corrosion 247
8.2 Corrosion Monitoring Techniques 248
8.3 Selecting a Technique for Corrosion Monitoring 248
8.4 Corrosion Monitoring Strategy 254
8.5 Measurement of Dissolved Solids 267
8.6 Measurement of Suspended Solids 267
8.7 Corrosion Product Analysis 267
8.8 Design Requirements 268
8.9 Automated Systems 270
8.10 Evaluation of Corrosion Inhibitors 273
8.11 Detection of Corrosion 275
8.12 Miscellaneous Corrosion Tests 278
8.13 Results of the Test Method 278
8.14 Field Testing of Inhibitors 279
8.15 Inhibitor Properties Other Than Effectiveness in Mitigating Corrosion 283
8.16 Monitoring of Corrosion Inhibitors 286
8.17 Corrosion Behavior of High-Alloy Tubular Materials in Inhibited Acidizing Conditions 288
9. Compatibility in Material Selection 295
9.1 Requirements for Compatibility 296
9.2 Structures and Equipment 300
9.3 Piping Systems 302
9.4 Fasteners 304
9.5 Encapsulation, Sealing, and Enveloping 306
9.6 Electrical and Electronic Equipment 306
9.7 Coatings, Films, and Treatments 308
9.8 Chemical Compatibility 310
9.9 Environment 311
9.10 Stray Currents 311
9.11 Beneficial Results 313
9.12 Shape or Geometry 313
9.13 Structures 315
9.14 Mechanics 322
10. Surface Preparation, Protection and Maintenance 337
10.1 Surface 337
10.2 Protection 350
10.3 Maintenance 373
10.4 Economics 376
11. Fabrication and Choice of Material to Minimize Corrosion Damage 385
11.1 Design 385
11.2 Materials 387
11.3 Fabrication 389
11.4 Welding Procedure 408
11.5 Welding and Joining 413
11.6 Soldered Joints 416
11.7 Brazed Joints 417
11.8 Pipe Bending and Forming 418
12. Heat Treatment 423
12.1 General Heat Treatment Requirements 423
12.2 Heat Treatment Process 427
12.3 Preheating of Metals 429
12.4 Surface Treatment of Stainless Steel 432
12.5 Handling, Transport, Storage, and Erection of Coated Metalwork 434
12.6 Inspection 437
12.7 Corrosion of Carbon Steel Weldments 438
Discussion 442
Conclusions 443
12.8 Corrosion of Austenitic Stainless Steel Weldments 444
12.9 Corrosion of Ferritic Stainless Steel Weldments 448
12.10 Corrosion of Duplex Stainless Steel Weldments 451
12.11 Stress-Corrosion Cracking 456
12.12 Use of High-Alloy Filler Metals 456
12.13 Corrosion of Nickel-Bases Alloys 456
Glossary of Terms 461
Bibliography 523
Index 535
School of Environment, Science and Engineering, Southern Cross University, Australia.