Micro / Nano Replication
Processes and Applications
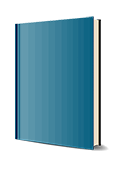
1. Auflage April 2012
384 Seiten, Hardcover
Praktikerbuch
Kurzbeschreibung
Micro and nano molding is a relatively new but fast-growing field that is impacting industries that use plastic parts in their products. Micro/Nano Molding introduces the fundamentals and processes for micro and nano molding for plastic components. This book also covers applications, details, and examples. Designed for industrial researchers, engineers and graduate students of polymer and mechanical engineering, this book helps readers understand and work with the growing tools of molding and uses for micro- and nano-sized plastic parts.
This book is an introduction to the fundamentals and processes for micro and nano molding for plastic components. In addition to the basics, the book covers applications details and examples. The book helps both students and professionals to understand and work with the growing tools of molding and uses for micro and nano-sized plastic parts.
* Provides a comprehensive presentation on fundamentals and practices of manufacturing for micro / nano sized plastics parts
* Covers a relatively new but fast-growing field that is impacting any industry using plastic parts in their products (electronics, telecommunications, biomedicine)
* Presents fundamentals and applications for both advanced students and professionals
* Presents the strengths and weaknesses of molding processes
1. Introduction 10
1.1 Introduction 10
1.2 Micro/nano replication 12
1.3 Application fields of micro/nano replicated parts 15
1.4 Required technologies for micro/nano replication 19
2. Patterning technology for micro/nano mold fabrication 27
2.1 Material removal 27
2.1.1 Mechanical machining 27
2.1.2 Laser ablation 28
2.1.3 Silicon etching process 29
2.1.4 Focused ion beam pattering 30
2.2 Lithography process 31
2.2.1 Electron beam lithography 31
2.2.2 Photo lithography 32
2.2.3 Reflow method 32
2.2.4 Laser interference lithography 38
2.3 Electroforming processes 42
2.3.1 Theory of electroforming process 43
2.3.2 Electroforming results 43
3. Modification of mold surface properties 51
3.1 Introduction 51
3.2 Study of thiol-based self-assembled monolayer 52
3.2.1 Thiol-based self assembled monolayer and deposition process 52
3.2.2 Experiment results and analysis 53
3.2.3 The changing properties of SAM at actual replication environment 54
3.2.4 Analysis of replicated polymeric patterns 56
3.3 Silane-based self-assembled monolayer (SAM) for nano master 57
3.3.1 Silane-based self-assembled monolayer 57
3.3.2 Deposition process of silane-based self assembled monolayer 58
3.3.3 Self-assembled monolayer on polymer mold 59
3.3.4 Analysis of replicated polymeric patterns 60
3.4 Dimethyldichlorosilane self-assembled monolayer for metal mold 60
4. Micro/nano injection molding with an intelligent mold system 63
4.1 Introduction 63
4.2 Effects of the mold surface temperature on micro/nano injection molding 64
4.3 Theoretical analysis of passive/active heating methods for controlling the mold surface temperature 65
4.3.1 Mathematical modeling and simulation 66
4.3.2 Passive heating 71
4.3.3 Active heating 73
4.4. Fabrication and control of an active heating system using a MEMS heater and an RTD Sensor 75
4.4.1 Construction of an intelligent mold system 75
4.4.2 Control system for the intelligent mold system 77
4.4.2.1 Kalman filter observer of the thermal plant 79
4.4.2.2 LQGI controller 81
4.4.2.3 Performance of the constructed control system 84
5 Hot embossing of microstructured surfaces and thermal nano imprinting 89
5.1 Introduction 89
5.2 Development of micro-compression molding process 90
5.3 Temperature dependence of anti-adhesion between a mold and the polymer in thermal imprintingprocesses 92
5.3.1 Defects in imprintedmicro optical elements 93
5.3.2 Analysis of polymer in process condition of thermal imprinting 93
5.3.3 Analysis of replication quality fabricated in different peak temperature 95
5.4 Fabrication of a micro optics using micro-compression molding with a silicon mold insert 96
5.4.1 Fabrication of microlens components using Si mold insert 96
5.4.2 Analysis of refractive micro lens 97
5.5 Fabrication of a microlens array using micro-compression molding with an electroforming mold insert 98
5.5.1 Fabrication of microlens components using Ni mold insert 98
5.5.2 Analysis of Replication quality 99
5.6 Application of micro compression molding process 100
5.6.1 Fabrication of a microlens array using micro-compression molding 100
5.6.2 Fabrication of metallic nano mold and replication of nano patterned substrate for patterned media 101
6 UV imprinting process and imprinted micro/nano structures 106
6.1 Introduction 106
6.2 Photopolymerization 106
6.3 Design and construction of UV-imprinting system 108
6.4 UV-transparent mold 108
6.5 Effects of processing conditions on replication qualities 110
6.6 Controlling of residual layer thickness using drop and pressing method 112
6.7 Elimination of micro air bubbles 113
6.8 Applications 114
6.8.1 Wafer scale UV-imprinting 114
6.8.2 Diffractive optical element 118
6.8.3 Roll to roll imprint lithography process 121
6.9 Conclusion 124
7 High temperature micro/nano replication process 128
7.1 Fabrication of metal conductive tracks using direct imprinting of metal nano powder 128
7.1.1 Introduction 128
7.1.2 Direct patterning method using imprinting and sintering 129
7.1.3 Mold and processing system 130
7.1.4 Defect analysis and process design 131
7.1.5 Analysis of imprinted conductive tracks 131
7.1.6 Conclusions 133
7-2 Glass molding of microlens array 134
7.2.1 Introduction 134
7.2.2 Fabrication of master patterns 135
7.2.3 Fabrication of tungsten carbide core for micro glass molding 136
7.2.4 Surface finishing and coating process of tungsten carbide core 138
7.2.5 Comparison of surface roughness before and after finishing process 139
7.2.6 Fabrication of glass microlens array by micro thermal forming process 140
7.2.7 Measurement and analysis of optical properties of formed glass microlens array 141
8. Micro/nano-optics for light emitting diodes 145
8.1 Designing an initial lens shape 146
8.1.1 LED illumination design 146
8.1.2 Source Modeling 147
8.1.3 Modeling a spherical refractive lens 147
8.1.4 Modeling a micro Fresnel lens 148
8.1.5 Verifying the micro Fresnel lens performance 149
8.2 Fabrication results and discussion 151
8.2.1 Fabrication of the micro Fresnel lens 151
8.2.2 Elimination of air bubbles 152
8.2.3 Optimization of the UV-imprinting process 152
8.2.4 Evaluation of the micro Fresnel lens for LED illumination 153
8.3 Conclusions 154
9. Micro/nano-optics for optical communications 158
9.1 Fiber Coupling Theory 159
9.2 Separated microlens array 161
9.2.1 Design 161
9.2.2 Fabrication 162
9.2.3 Measurement results 163
9.3 Integrated microlens array 166
9.3.1 Design 166
9.3.2 Fabrication 167
9.3.3 Measurement results 168
9.4 Conclusions 170
10. Hard Disk Drive (HDD) 173
10.1 Introduction 173
10.2 Fabrication of a metallic nano mold using a UV-imprinted polymeric master 175
10.3 Fabrication of patterned media using the nano replication process 181
10.4 Fabrication of patterned media using injection molding 184
10.5 Measurement and analysis of magnetic domains of patterned media by magnetic force microscopy 187
10.6 Conclusions 190
11. Optical Disk Drive(ODD) 194
11.1 Introduction 194
11.2 Improvements in the optical and geometrical properties of HD-DVD substrates 196
11.3 Effects of the insulation layer on the optical and geometrical properties of the DVD mold 199
11.4 Optimized design of the replication process for optical disk substrates 202
11.5 Conclusions 206
12. Biomedical applications 209
12.1 Introduction 209
12.2 GMR based protein sensors 210
12.2.1 Principle of GMR protein sensors 210
12.2.2 Principle of guided mode resonance effect 210
12.2.3 Nano replication process of a GMR protein chip for mass production 213
12.2.4 Feasibility test of GMR protein chip 217
12.3 Conclusions 218